Between Denmark and Sweden lies the Øresund Strait, where the brackish waters of the Baltic Sea mingle with the Atlantic Ocean.
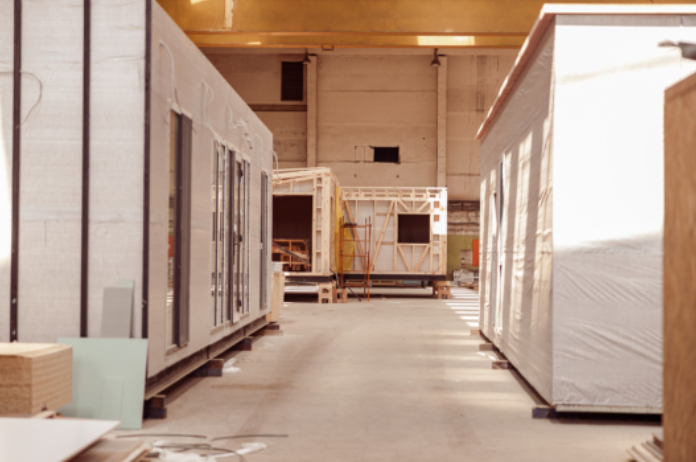
Spanning the strait is the Øresund Bridge (in Swedish, that “o” with the slash through it sounds like the “u” in the English word “blue”). Built in 1995, this cable-stayed suspension bridge of steel and concrete supports both rail and automobile traffic, with an estimated 20,000 commuters traversing its length back and forth each day. It has become a symbol–albeit a sometimes fraught one–of positive relations between the two nations.
Even at five miles long, the Øresund Bridge isn’t all that remarkable for its size. The Danyang-Kunshan Grand Bridge in China, for instance, is 20 times longer, reaching 102 miles across the wetlands of the Yangtze River delta. Nor is Øresund’s conservative design anywhere near as interesting to look at as the medieval Ponte Vecchio bridge in Florence, the living root bridges of northeastern India, or the sweeping neo-futuristic lines of the Zubizuri foot bridge in Bilbao, Spain. No. What makes the Øresund Bridge unique is how it was built: Pre-fabricated in an off-site factory…that and the fact that it turns into a tunnel (!) halfway across. Terminating abruptly at the edge of an artificial island in the middle of the strait, the bridge appears from a distance to lead to absolutely nowhere at all.
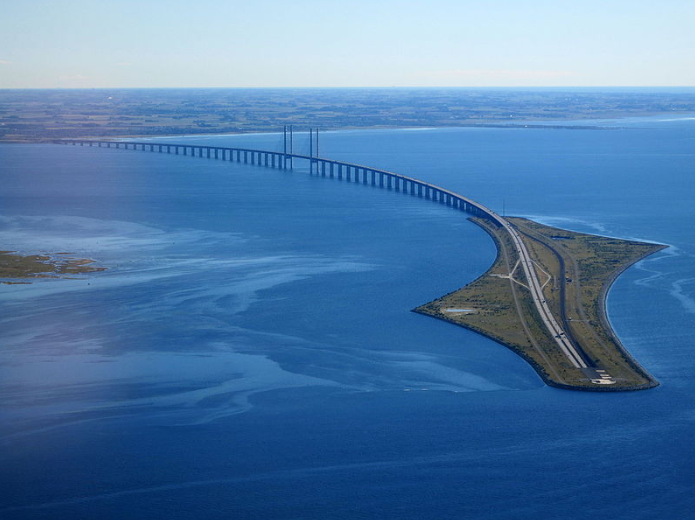
Okay, that last detail is undeniably a bit more of a show-stopper than how the thing was built. Nevertheless, the impressive engineering of a Nordic bridge that casually swan-dives into the sea and, yes, transforms into a 2.5-mile-long underwater tunnel isn’t actually the focus of this article. What we’re going to talk about instead is the approach to building and design that made this and many other incredible projects possible: a method called offsite construction. In this article, we will explain what offsite construction is, provide some brief historical context, examine why it’s on the rise, explore some of the forms it takes, identify some of the obstacles in its path, and take a look at what the future holds for offsite construction.
What Is Offsite Construction?
Off-site construction is the process of planning, designing, fabricating, and/or assembling a structure at a location other than where the final structure will ultimately be installed.
What Is the Difference between Onsite and Offsite Construction?
Offsite construction, different from traditional construction which typically involves the piecemeal assembly of building components at the site of the final product, offers a form of construction automation. Preassembly of building components are completed somewhere offsite from the final building place and are often outsourced to third-party manufacturing partners. Critically, offsite construction is less concerned with the setting and idiosyncrasies of individual projects, opting instead to focus on forms that can be easily replicated and mass produced independent of a specific location. In this sense, offsite construction takes a page from the playbook of the modern industrial manufacturing process, with its wide-open factory spaces and automated assembly lines that generate reliable outcomes.
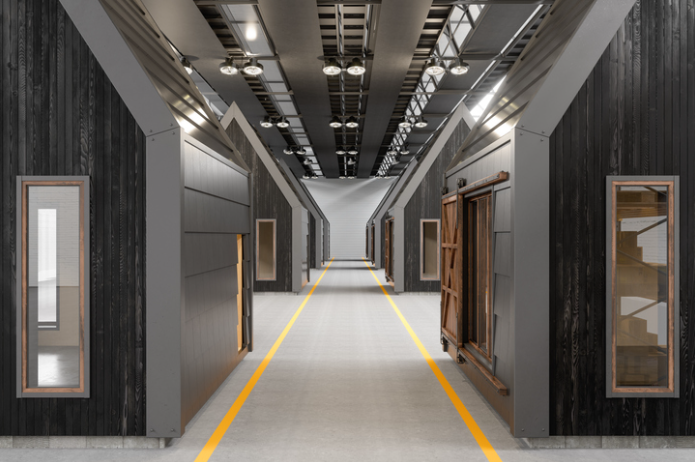
To illustrate what offsite construction looks like and why it’s preferable in some cases to the traditional method, let’s return for a moment to the Øresund Bridge. The project’s designers weren’t just showing off when they chose to use a bridge-tunnel hybrid. A bridge all the way across the strait would have presented a significant risk of airplane collisions from the nearby Copenhagen airport. A tunnel, while more challenging to pull off, would keep the airspace clear and avoid this risk entirely. The engineers needed the submerged concrete to be of a consistent quality and have the highest level of protection against cracking. The best way to achieve this degree of precision was to pour each of the tunnel’s 72-foot-long segments in a single phase within the more easily controlled indoor environment of an offsite factory. A similar prefabrication process was then followed to manufacture the bridge’s caissons and piers. The result was a true marvel of technology and engineering, completed within budget and several months ahead of schedule.
A Brief History of Offsite Construction
While offsite construction might seem like a contemporary development, it isn’t anything new. Companies like Sears, Roebuck & Co. were selling “kit homes” out of the pages of printed catalogs as early as the 1800s. Fitting a pre-designed floor plan with limited customization options, the construction materials would be shipped off and delivered to the purchaser, who could then assemble it piece-by-piece on-site. Though these early kit homes eventually vanished, more sophisticated modern versions can still be purchased to this day.
Offsite builders have also offered their services in building unique shipping container homes.
Why Is Offsite Construction on the Rise?
Offsite construction has experienced a bit of a renaissance in recent years. A 2018 survey of construction companies conducted by the National Institute of Building Sciences’ Offsite Construction Council (OSCC) showed that 87% of all respondents reported using offsite constructed components over a 12-month period. About 53% of commercial builders utilized offsite construction, with multi-family and single-family housing developers reporting 38 and 18% utilization, respectively.
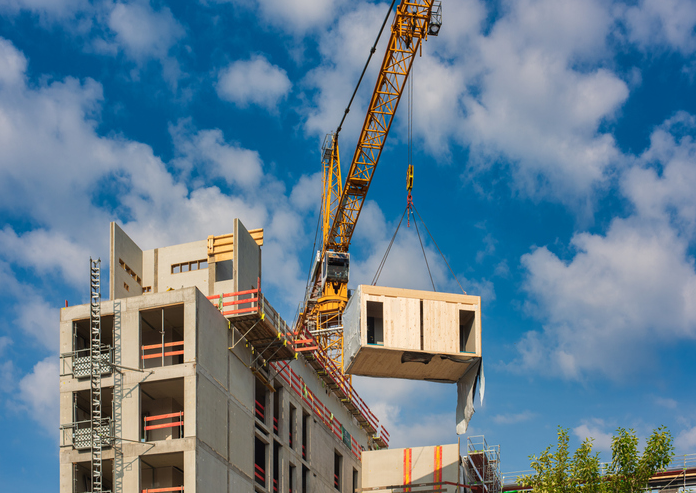
The buzz in some industry circles is that offsite construction is a potential solution to a range of problems that plague the industry–chief among them being a shrinking workforce, dangerous work environments, and a lack of reliable outcomes (for instance, whether projects will be consistently delivered on time, within budget, and to exact specifications). These symptoms and many more are the subject of an influential 2016 report by Mark Farmer, a CEO of a construction consultancy firm based out of the United Kingdom. In the report–evocatively entitled “Modernise or Die”–Farmer argues that the construction industry is “in dire need of change” and that business as usual “is simply not an option.” One of the seismic shifts he recommends is for industry leaders to embrace offsite construction. Here’s Farmer:
“If you buy a new car, you expect it to have been built in a factory to exacting standards, to be delivered on time, to an agreed price and to a predetermined quality. This needs to happen more in construction…There are more similarities between manufacturing and construction than many people are led to believe and this perception needs to change, starting in the housing market.”
Types of Offsite Construction: 3 Applications
The idea behind offsite construction is to introduce standardization into the building process. Since no two building projects are exactly the same, there are multiple ways to approach offsite construction. Let’s take a closer look at 3 approaches now:
- Modular construction
- Prefabricated construction
- 3D printing
Modular Construction
Modular construction is a method of designing and assembling buildings in offsite facilities in repeatable sections or rooms called modules that are then delivered to a jobsite to be installed. This process allows for the rapid construction of temporary structures or permanent buildings with simple floorplans that follow uniform patterns such as apartment complexes, healthcare, educational, or public facilities. Tiny homes are an easily recognizable example of modular construction.
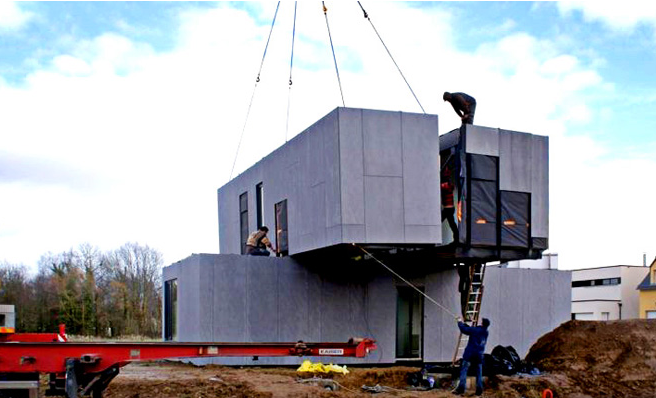
Prefabricated Construction
Prefabricated construction–also referred to as prefab–is another popular offsite approach. Or, in some cases, companies build a fabrication site on or adjacent to the job to streamline the prefab process. Where modular focuses on the delivery of entire buildings or rooms of buildings, prefab specializes in the manufacture of individual components that can then be installed like Legos to create a whole structure. Using this process, builders can order finished items like roof trusses, staircases, and walls (complete with insulation, vapor barriers, and wiring), or opt instead to purchase open “panels” that can then be modified onsite. A common usage of prefab construction involves the assembly of precast concrete walls and flooring to create the shell of a long-lasting structure.
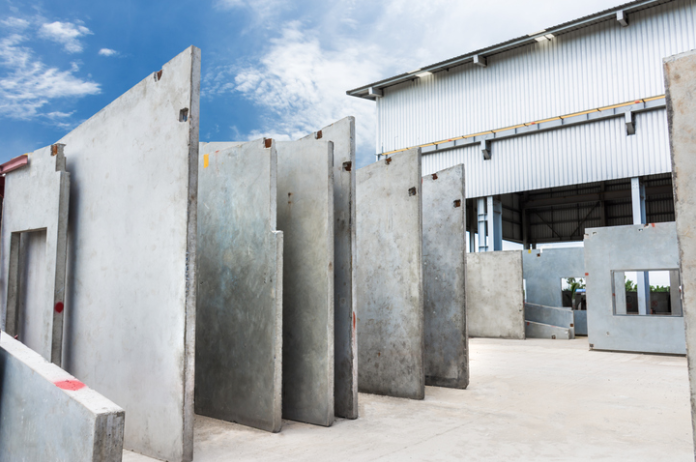
MEP prefab, the most prevalent offsite construction, is focused on the process of using and modifying standardized parts and components to construct assemblies using one or more processes.
Examples include:
- Pipe hangers
- Trapezes
- Duct banks
- Whips
- Pre-cut, pre-bent conduit
3D Printing
3D printing has emerged as a viable method of mass producing replicable structures in recent years. A still young technology, it can already be used to print individual construction components or even entire buildings. This approach can also be deployed onsite, though the advantages of offsite applications are still manifest: it’s easier to assemble and operate 3D printing applications to generate prefabricated building components in the climate controlled setting of an offsite factory, where uneven surfaces and other environmental irritants aren’t a factor.
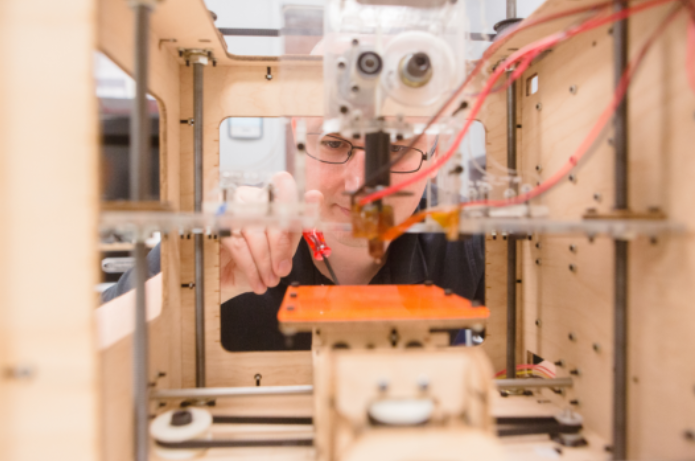
Other Forms of Construction Automation and Process Improvements
Offsite construction methods are often used in conjunction with other forms of construction automation and technology to improve workflows.
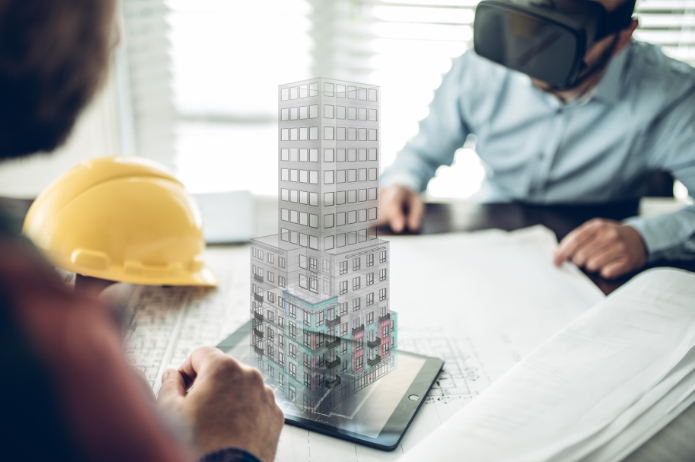
Here are a 6 forms of construction automation outside of offsite construction:
- Construction robots are poised to become an increasingly common tool in the repertoire of offsite construction techniques employed by savvy construction technologists. Just as with manufacturing before, robots are now able to perform a wide variety of building activities such as welding, bricklaying, and 3D printing. In the years ahead, more and more of the prefabricated components coming out of offsite construction factories will be created with the aid of automated helpers, on and off the jobsite.
- Building information modeling (BIM) is often used by architects, designers, and BIM specialists alike to coordinate design blueprints digitally. These models can be used as a risk management tool to avoid rework when shared with clients, as they’ll visualize and bring to life these blueprints for them in rich built environments. What’s more, as projects grow from single buildings to whole cityscapes, City Information Modeling (CIM) comes into play.
- Light detection and ranging (LiDAR) technology can be used for land surveying and structural analysis, as well as in conjunction with BIM to provide an extra layer of real-time analysis.
- A geographical information system (GIS) can be used for land and terrain surveying and quality inspection, helping to determine the viability and sustainability implications of building on a given site.
- Construction drones can be used to improve workflows from as early as surveying potential issues onsite remotely to well into the construction process by helping owners ensure work is being performed safely and to spec.
- Digital inventory management: There are many advantages for contractors to use an inventory app like One-Key. Digitizing the inventory process can help reduce costly downtime, as well as be used to solve industry-wide labor shortages. But what’s more, an inventory app like One-Key can be used in conjunction with BIM to ensure project data syncs up and all teams are on the same page.
What Are the Benefits of Offsite Construction?
We’ve already hinted at some of the advantages conferred by offsite construction. By mimicking manufacturing processes, the construction industry can become a leaner, smarter, and more sustainable machine capable of producing reliable results that are consistently on time and within budget. There’s a reason–a few, actually–why industry leaders are heralding offsite construction as a revolutionary sea change.
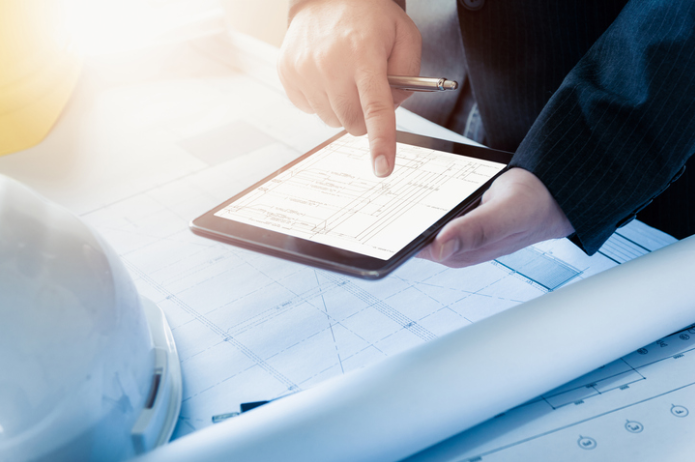
Here are 5 of the key benefits and selling points that make offsite construction so attractive:
- Speed
- Saves money
- Quality assurance
- Safer and better work environments
- Environmentally friendly
Let’s dive into each of these.
1. Speed
Offsite construction is faster than traditional construction, which is known for delivering projects behind agreed-upon deadlines. This was one of the key findings of the OSSC survey cited above: Respondents agreed that their projects got done a lot faster when building offsite. When building onsite, workers are at the mercy of a wide range of variables that can throw a wrench into even the best laid plans: Poor weather, overbooked schedules, unreliable subcontractors, unpredictable change orders, snares in the supply chain–all of these can cause massive delays. Designated crews working on replicable sets of prefabricated components and modules–perhaps aided by robotic assembly lines and 3D printers–in the controlled environment of an offsite factory aren’t plagued by these issues. As a result, they’re able to get the same amount of work done in a fraction of the time. Indeed, a recent report by McKinsey showed that the modular approach to offsite construction can accelerate a project’s timeline by as much as 20 to 50%.
2. Saves Money
The same survey referenced above also notes increased cost effectiveness among companies that utilize offsite practices. At the end of the day, it’s easier to plan, design, and fabricate reliable outcomes when the idiosyncrasies of an onsite setting are removed from the picture. Factory production of construction components simply removes delays and unpredictability from the equation, which adds up to dollars saved. Put more concretely, the previously mentioned McKinsey report also shows that modular construction can lead to budgetary savings of up to 20%.
3. Quality Assurance
Offsite construction factories can guarantee that building components are generated to exact specifications time and time again. In an offsite setting, workers follow established templates and procedures geared toward standardization, ensuring a consistent level of quality across the board. What’s more, the controlled offsite setting allows for the end products to be subjected to a greater degree of scrutiny and review compared to onsite operations.
4. Safer and Better Work Environments
Construction sites are notoriously dangerous places. Workers are safer in offsite factories, where many of the hazards that can cause grievous accidents or even death are absent from the picture. Workers also don’t have to contend with the weather or long commutes to and from different jobsites or other trades.
5. Environmentally Friendly
Offsite construction dramatically reduces the footprint of a construction site. Less space is taken up by heavy equipment and less time is needed to assemble the final product. The precise nature of an offsite build also leads to less waste being generated.
What Challenges Does Offsite Construction Face?
With the advantages that offsite construction offers, it can be easy to forget that it's not without its challenges. Let’s take a look at a few of the barriers that offsite construction will need to overcome in the years ahead:
- Stigma: There’s a stigma attached to terms like “prefabricated,” conjuring images of cheaply built materials and cookie cutter structures. While this can sometimes be the case, cheap materials are certainly not inherent to the offsite construction process. As the Øresund Bridge exemplifies, offsite construction is capable of producing dynamic structures engineered and built with materials held to the highest standards of quality.
- Transportation: A majority of the OSCC survey respondents noted that the distance between the offsite factory and the location of final installment can sometimes be a source of headaches.
- Culture: One of the most significant barriers to implementing offsite solutions identified in the OSCC survey is the deficit of a collaborative culture in construction and design circles.
- Building Codes: Many building codes are geared toward onsite practices and haven’t caught up to changing paradigms. Depending on the location of a project, outdated codes get in the way of offsite construction utilization. The good news is that the International Code Council is aware of the problem and has begun to respond.
The Future of Offsite Construction
There may be challenges but offsite construction is clearly gaining momentum. The need for greater efficiency, more reliable outcomes, heightened sustainability, and safer work environments will continue to drive the embrace of offsite construction by more and more industry leaders in the years ahead. And if they won’t do it willingly, their clients will compel them to. Major companies like McDonalds and Marriott International have turned to offsite construction in recent years to construct their buildings within a speedier and more consistent time frame. Game-changing technologies like Building Information Models (BIM) are also making it easier than ever for disparate team members to collaborate and direct the design of prefabricated components and modules in offsite operations. It’s clear that offsite construction is set on an upward trajectory. What remains to be seen is how rapidly the construction industry as a whole will adapt to the changing paradigm.